Renovation and Upgrading of Hydroforming Machine
In February (Week 8), a hydroforming machine was dismantled from a customer in Germany specializing in the manufacturing of exhaust components, including pipes for exhaust systems primarily for German-made passenger cars. The purpose of the dismantling was to carry out extensive renovation and prepare the machine for resale.
The machine was originally designed in 2001 and has been in the customer’s production facility since 2003. Over the years, it has been operated in three shifts, delivering high-quality exhaust systems to some of the most prominent European car manufacturers.
The renovation work is expected to take approximately 10-12 weeks, which is significantly shorter than the original construction time of around 30 weeks.
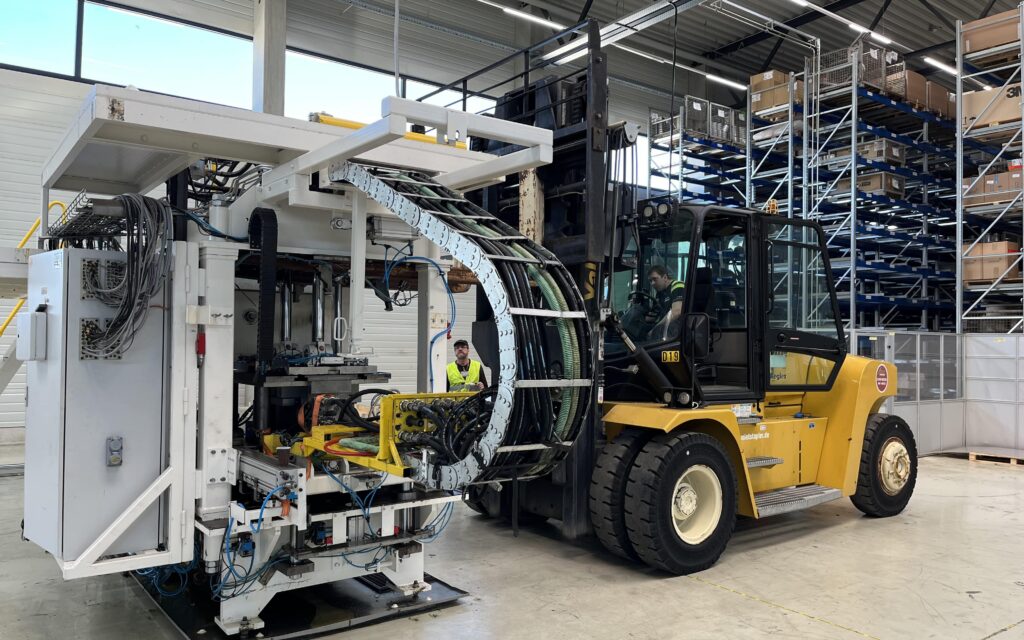
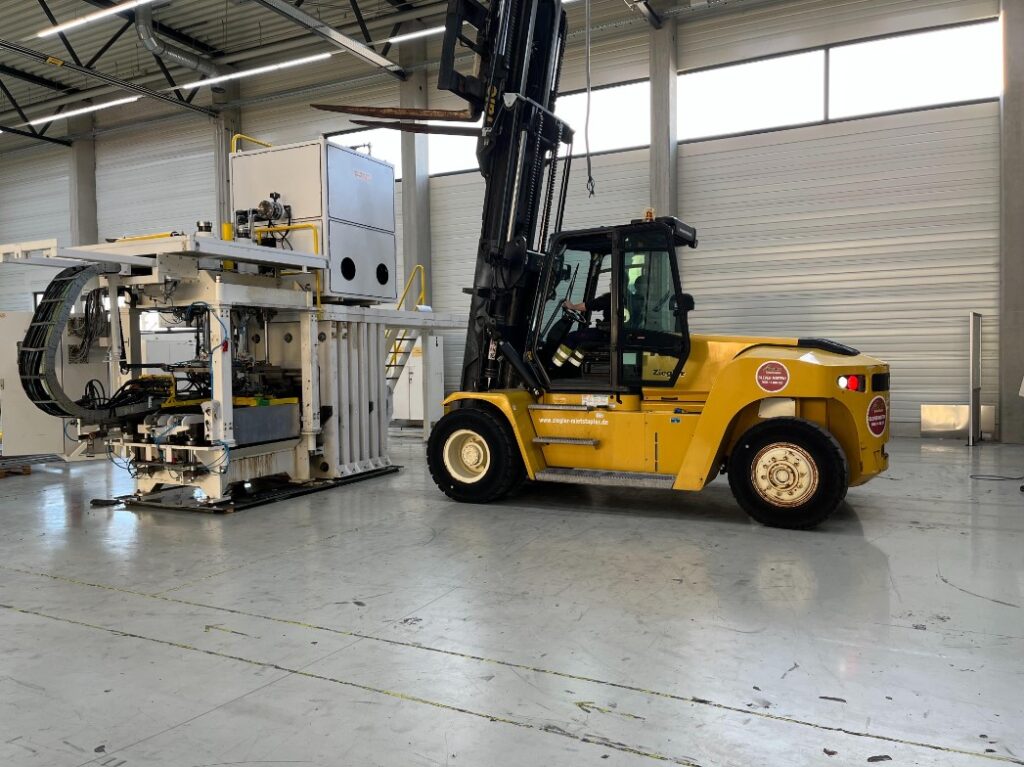
The plan is to use the machine in the future for manufacturing both car and truck exhaust systems. When producing pipes for trucks, typically more power is required due to the larger diameter and length of the pipes.
The new machine being built will provide the customer with the capability to switch between manufacturing exhaust systems for both cars and trucks daily. The tool changeover can be accomplished in less than 10 minutes, which is known as SMED (Single Minute Exchange of Die), a method for rapid tool changeovers.
As part of the renovation, the machine will be repainted from white to blue. Additionally, a thorough inspection will be carried out, and any necessary welding or repairs to existing parts will be performed.
In the previous version of the machine, an air cylinder was used for tool movement, but in the upgraded version, a hydraulic motor will be employed. This change is being made to reduce cycle time and facilitate the movement of the tool. Currently, the tool, which can weigh up to 5 tons, is moved using an air cylinder. This method will be replaced with a chain driven by a hydraulic motor. By using hydraulics instead of air, the process becomes simpler and safer.
As part of the upgrade, the machine will be equipped with modern software to streamline costs and enhance performance. This includes an improved Human-Machine Interface (HMI) for better user interaction. The entire PLC system will also be replaced to enable more precise positioning through faster and more accurate calculations. This technological enhancement aims to optimize the machine’s capabilities and increase overall efficiency.